Chemicals
Managing hazardous materials in a responsible way
Waste & Chemicals
OUR AMBITION
Strive for zero waste in landfill, reduce our consumption of chemicals and eliminate hazardous materials.
2025 GOAL
95%
of our waste reused and recycled
ST takes a precautionary principles approach to responsibly managing chemical substances and materials, to protect people and the environment and comply with customer and legal requirements.
All chemicals used on site are evaluated before being used. The evaluation focuses on the composition, the hazards and the use conditions, including risk management measures, personal protective equipment, waste management and administrative controls. Thanks to this continual process, critical substances are identified as soon as they are introduced or reclassified. In 2019, we recorded 5,896 chemicals in use, and we conducted 815 new risk assessments, reaching a total of 29,408 validated risk assessments by the end of the year. I 103-2 I 103-3 I
5,896
chemicals in use
Preventing human exposure to chemicals
We implement programs on all sites to improve safety during chemical handling and to reduce employee exposure. We continue to strengthen the safety of equipment and controlled conditions. For example, our Tours (France) and Agrate (Italy) sites developed specific medium-term programs to upgrade or replace equipment and minimize manual handling, thereby limiting the potential exposure of employees and improving safety levels.
The 10,326 industrial hygiene measurements we performed during the year were all below the applicable limits, demonstrating the effectiveness of our mitigation actions.
2019 OBJECTIVES |
Status |
Comments |
|
In line with WSC statement, remove PFOA and PFOA-related substances in all manufacturing chemicals by 2025. |
|
Removed 94.4% PFOA and PFOA-related substances in 2019 compared to 2014 when the program started. |
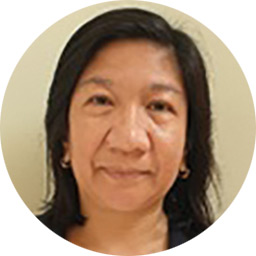
Hahnsen L. Isidro
President and GM
STMicroelectronics is a leading semiconductor company in the Philippines recognized for its egalitarian approach to suppliers. Its robust accreditation privileges are bolstered by its desire for supplier companies to mirror its technical expertise and to provide only the best quality products and services. It is continually looking to improve efficiency by the use of new technologies and systems. Quimicos is committed to supporting STMicroelectronics to accomplish new goals in the future.”
Replacing hazardous substances
At each manufacturing site we implement programs to consider chemical use and potential alternatives, whenever possible.
After seven years of work and tests, our Rennes site (France) successfully identified a resin to substitute the substance MHHPA (hexahydromethylphthalic anhydride), a well-known and widely used component of hard resins. It has been included in the SVHC(1)candidate list since December 2012 due to its respiratory sensitizing properties(2).
Substituting
chemicals
We use this resin to test the reliability of samples of a product for the medical market. When the testing is complete, the final product – which does not contain the resin itself – is delivered to the customer. Even though there is no resin in the final product, we believe it is important to find an alternative, while also excluding substances that could potentially face restrictions in the future.
For each resin, we conducted many reliability tests to validate the process. In 2019, we finally identified one suitable resin. We will therefore use a different resin in 2020, once the customer approves the process change.
During 2019, we continued to work on phasing out PFOA (Perfluorooctanoic acid) related substances in line with our commitment. However, we have not yet completed the replacement plan for the DEHP (Di-ethylhexyl phthalate) contained in wafer tapes.
Where there is no alternative to using hazardous substances, we take precautionary measures to prevent any adverse impact on people and the environment. We also proactively work with chemical manufacturers on replacement plans. We are currently doing this for a specific nonylphenol used in both a back-end plating solution and a laboratory solution for medical diagnosis. This substance is already listed under Annex XIV and included in the SVHC candidate list. We also ensure usage occurs under adequate risk management measures, so there is no potential exposure to employees.
Our Calamba site (the Philippines) is one of the largest users of water and chemicals among our back-end sites. It therefore introduced a program to reduce consumption of these resources. To reach the challenging environmental goals, the site’s facilities team looked for an alternative to reverse osmosis feed-water pretreatment, part of the process to generate ultra-pure water (see Water).
Using less
chemicals and water
A new product, a type of antiscalant, was introduced to replace the water softener. As the antiscalant prevents scaling and fouling, it helps maintain the membrane surface cleaner and therefore reduces the need for water. The elimination of the water softener reduced the use of water during the regeneration process by 4% (around 47,000m3 per year) and reduced the use of chemicals by 68% (around 363,000kg per year) compared to 2018, without affecting the quality of the water supplied for the manufacturing processes. This was only possible thanks to an extensive collaboration with the chemical provider (see quote).
Adhering to the highest standards
We aim to ensure that all chemicals used in ST operations and products are legally authorized and meet customer requirements.
Complying with legal requirements
We comply with applicable environmental regulations and requirements, including European chemical policies and directives such as REACH(3), RoHS(4), and ELV(5). Over the last two years, ST’s chemical experts have jointly worked with suppliers and car manufacturers to renew the exemption to the ELV Directive for the use of lead in high melting temperature solders, due to there being no suitable alternative. At the end of 2019, the European Commission granted the extension of this exemption while work continues to identify suitable alternatives, leading the industry into the next phase of the lead-free semiconductor evolution.
Reducing hazards
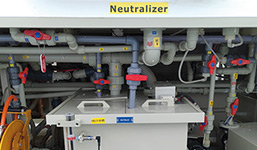
FOCUS
Identifying a safer alternative
Our Shenzhen site (China) implemented a project to eliminate hazardous liquid waste generated by the plating line process, a step in the manufacturing process.
Before 2019, the neutralizer used in one of the process steps generated hazardous liquid waste which we could not treat on site. Taking into consideration the impact of our activities on both people and the environment, the teams focused their efforts on finding a more suitable and effective solution.
Experts identified one neutralizer solution among four preselected, ensuring it would not impact the manufacturing process or the product quality. As a result, the chemical liquid waste now generated by the process is treated on site and is no longer hazardous.
Meeting customer expectations
To provide our customers with information on the chemical composition of all our products, we report and publish our material declarations (available at www.st.com) in accordance with the IPC1752(6) standard.
In 2019, as in previous years, our customers maintained a high level of interest in the way we manage chemicals. Seven customer audits were conducted throughout the year at our sites in Shenzhen (China), Calamba (the Philippines) and Ang Mo Kio (Singapore). The results demonstrated a good level of chemical management. All three sites received positive feedback from customers, who recognized a continuous improvement.
Positive feedback
from customers
ST still pursues the implementation of Hazardous Substance Process Management (HSPM) to identify, control, qualify and report any dangerous element in component products according to the QC080000 standard.
We require our suppliers to respect our EHS-regulated substances list, which contains more than 3,000 substances and is regularly reviewed. We also require them to confirm their compliance through analytical certificates, safety datasheets and commitments.
Contributing to the Sustainable Development Goals
Our commitments and programs as described above contribute to:
SDG target 3.9 – Substantially reduce the number of deaths and illnesses from hazardous chemicals and air, water and soil pollution and contamination.
SDG target 6.3 – Improve water quality by reducing pollution, eliminating dumping and minimizing release of hazardous chemicals and materials, halving the proportion of untreated wastewater and substantially increasing recycling and safe reuse globally.
SDG target 12.4 – Achieve the environmentally sound management of chemicals and all wastes throughout their lifecycle, in accordance with agreed international frameworks, and significantly reduce their release to air, water and soil in order to minimize their adverse impacts on human health and the environment.
(1) SVHC: Substance of Very High Concern.
(2) https://echa.europa.eu/documents/10162/3ee8978c-40be-4dc4-a12d-798caf6424f0
(3) REACH: Registration, Evaluation, Authorization and Restriction of Chemicals.
(4) RoHS: Restriction of Hazardous Substances.
(5) ELV: End of Life of Vehicles.
(6) IPC1752: Association connecting electronics industries.