Responsible Supply Chain
Supply chain responsibility in challenging times
Responsible Supply Chain
Our Ambition
Systematically assess and mitigate social, environmental, health & safety, and ethical risks in our extended supply chain.
2025 GOAL
100%
suppliers at risk audited
133/800 suppliers audited.
In complex supply chains such as those within the electronics industry, the COVID-19 pandemic poses a greater risk to vulnerable workers. We have therefore been extra vigilant in maintaining robust control of our supply chains. We also re-emphasized our pledge to partner only with suppliers who share the same values of respecting people and acting ethically.
RBA standard
and tools deployed in our supply chain
We adapted our main Responsible Supply Chain program, which addresses labor, human rights, safety, ethics and environmental risks in our tier 1 supply chain, to reflect national restrictive measures. This included conducting audits remotely.
Our program is based on the Responsible Business Alliance (RBA) methodology, adopted in 2005 and deployed progressively in our supply chain since then. It comprises three main steps:
28
preliminary risk assessments analyzed on CSR criteria
In 2020, we reinforced our preliminary risk assessment process for new material suppliers. We focused on environmental and safety certifications and detecting forced labor, with specific actions for poor performance.
In addition to the program for our tier 1 suppliers, we also manage our sub-tier raw material suppliers (see Responsible mineral sourcing section). I 103-1 I 103-2 I
Actions for all categories of suppliers
As a company with more than 6,000 tier 1 suppliers, it is important for us to identify and prioritize suppliers at risk to include them in our due diligence process. Our annual risk assessment considers the type of supplier, the location of their operations (or a specific factory) and the volume of business they do with us.
We adapt our level of due diligence to the two different categories of suppliers we manage:
- Direct manufacturing suppliers including manufacturing subcontractors, material suppliers and equipment and spare-parts suppliers. This segment represents the highest percentage of ST’s procurement volume (78%).
- Indirect services including local suppliers such as catering, security, labor agencies and facilities management, which represent 22% of our procurement volume.
Our suppliers I 102-9 I
Procurement volume
37% of our procurement volume is managed locally. The rest is managed centrally at corporate level. I 204-1 I
265 RBA-based supplier audits since 2015,
+49%
vs 2019
We monitor each category through the three-step process of our Responsible Supply Chain program. We define which suppliers are eligible for each step based on their level of risk and adapt the level of due diligence accordingly.
Overall, for both direct and indirect suppliers, 95% of eligible tier 1 suppliers have signed a commitment letter (step 1). In total, since the start of the program in 2015, our suppliers have undergone 265 RBA-based audits (step 3), +49% compared to 2019.
Direct manufacturing suppliers
- 93% of 181 eligible suppliers have signed a commitment letter and 97% of new direct suppliers have undergone a screening process, including social, environmental, and health and safety criteria.
- 90% of 369 eligible supplier facilities have completed a self-assessment questionnaire (SAQ). 92% are rated low risk and 8% are medium risk.
- 9% of 369 eligible supplier facilities have undergone a third-party RBA VAP audit over the past two years, up from 7% in 2019.
Top 5 audit findings in our direct manufacturing supply chain(1) I 308-2 I 414-2 I
Indirect service suppliers
- 98% of 154 eligible suppliers have signed a commitment letter and 99% of new indirect suppliers have undergone a screening process, including social, environmental, and health and safety criteria.
- 79% of 126 eligible suppliers have completed an SAQ, up from 44% in 2019 (with a smaller number of eligible suppliers).
- 79% of 126 eligible suppliers have undergone a second-party RBA audit (conducted by ST) over the past two years, up from 31% in 2019. In 2020, we integrated more environmental and health and safety criteria for local audits and we also verified protection measures against COVID-19.
Top 5 audit findings in our indirect services supply chain(1) I 308-2 I 414-2 I
In addition, we regularly evaluate our suppliers’ performance on social, environmental, and health and safety criteria, and we deploy specific programs to address environmental and safety topics (see Health and Safety and Chemicals).
In 2020, 82% of our key suppliers were ISO 14001 certified or EMAS validated, up from 76% in 2019. I 103-3 I
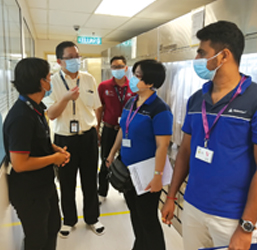
Focus
Protecting vulnerable workers
In every action we instigate in our supply chain, our priority is to detect and address the most severe impacts for vulnerable workers. We have a zero-tolerance policy towards forced labor and we maintain strict control of working hours and wages to ensure decent living conditions and avoid any risk of coercion.
In 2020, we focused on addressing some of the most impactful risks we had detected:
- Impact of lockdowns on foreign migrant workers in Malaysia due to the pandemic. We communicated with direct manufacturing suppliers to verify that salaries were maintained to ensure basic needs and that annual leave entitlements were not affected.
- Recruitment fees for foreign migrant workers in Taiwan. We launched a zero-recruitment fees campaign with five suppliers to accelerate their adoption of a zero-fee recruitment policy.
- Supplier corrective actions for priority findings on forced labor. We closely monitored the corrective actions for priority findings involving foreign migrant workers, such as reimbursing fees, payment of incomplete wages and contract substitution, requiring suppliers to complete their closure audits within the year.
Addressing such systemic and complex issues may be challenging, but we have noticed an increasing willingness to collaborate and improve the overall situation from our suppliers.
Supporting our suppliers towards compliance
We are not only committed to controlling our suppliers, but also to supporting them in raising their awareness and capability to comply with required standards.
Our aim is to help our suppliers improve their performance sustainably, through dedicated e-learning on risks in areas such as labor (including working hours and forced labor), ethics, health and safety, environment and management systems.
Customized
learning paths
for suppliers
As well as the customized supplier e-learning paths we launched in 2019 through the RBA platform; our worldwide community of experts supports suppliers’ continuous improvement through ongoing dialog and sharing best practices.
For example, at ST Bouskoura (Morocco), after encountering difficulties in reducing the working hours of security services below 72 hours per week, we launched a new bidding process that included criteria for working hours compliance. In 2020, we chose a new service provider and, by working closely together, we were able to reduce working hours to 60 hours per week, with a strong positive impact on workers’ lives (see quotes).
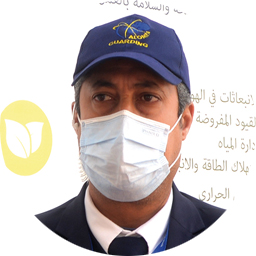
Khmessi Said
Security agent, Alomra – security supplier in ST Bouskoura (Morocco)
This change has had a very significant and positive impact on my personal life. Previously, I left the house while my children slept (5 a.m.) and by the time I got home (10 p.m.), my children were already in bed. Now, I have time to see my children grow up, and to play with them. I have a life!”
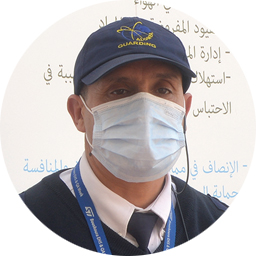
Benaamar Jamal
Security agent, Alomra – security supplier in ST Bouskoura (Morocco)
The moment ST did the audit and we understood that among the RBA requirements there was a 60-hour working week restriction, we said to ourselves, it will be a miracle if ST manages to change this, as it is general practice for the security sector in Morocco. Now, we are very confident in this system and we are very grateful that ST has been able to change this unfair practice. It has led to numerous positive changes in our personal and professional lives. It was a dream that came true.”
We also organized online meetings to share best practices between our sites in Malaysia and China and some major manufacturing suppliers. Topics included how to better manage working hours and how to organize supply chain controls.
Responsible mineral sourcing
Our approach to supply chain responsibility goes beyond our tier 1 suppliers. It also covers the responsible sourcing of raw materials in our upstream supply chain.
100%
of our 3TGs smelters validated through the Responsible Minerals Assurance Process
In 2020, we had 239 smelters in our tin, tungsten, tantalum and gold (3TGs) supply chain. For the fourth consecutive year, we successfully validated all of them through the Responsible Minerals Assurance Process.
We usually eliminate smelters when they cease operation, although in 2020 we also had some cases where non-compliance led to their certification not being renewed.
As an active participant in the Responsible Minerals Initiative (RMI), we also began to monitor our cobalt supply chain in 2019, as concerns have been raised globally over the social and environmental impacts of cobalt extraction, including child labor and unsafe working conditions in artisanal cobalt mining. However, due to a lack of existing regulations on cobalt, progress on smelter certification is relatively slow.
For more detailed information on our progress, see www.st.com/conflict-free_minerals.
Contributing to the Sustainable Development Goals
Our commitments and programs related to Responsible Supply Chain as described above contribute to:
SDG target 8.7 – Take immediate and effective measures to eradicate forced labor, end modern slavery and human trafficking, and secure the prohibition and elimination of the worst forms of child labor.
SDG target 8.8 – Protect labor rights and promote safe and secure working environments for all workers.
2020 OBJECTIVES |
Status |
Comments |
|
≥90% of eligible suppliers signed an agreement to comply with the RBA code of conduct. |
|
95% |